Entries tagged with “training”.
Did you find what you wanted?
Tue 5 Nov 2013
Posted by admin under Federal OSHA, GHS, Hazard Communication, Management, MSDS, OSHA, Personal Protective Equip (PPE), Safety Programs, SDS, Training, Uncategorized
Comments Off on Hazard Communication with GHS – SDS/MSDS
If you live in the United States, you have less than one month to train your employees on the new Hazard Communication standard (1910.1200(h) & 1926.59), which should include information about the new types of Safety Data Sheets (formerly known as MSDS) and the adaptation with the Global Harmonization System (GHS). December 1, 2013 is the enforcement start date for OSHA. Don’t make this complicated, it is straightforward. Here’s what you should do:
- Train employees in hazard communication (simply: so they know the hazards they are working with)
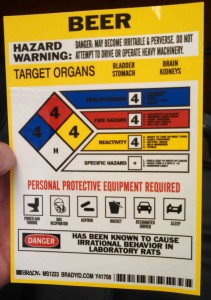
- Document your training (in case of an OSHA inspection)
- Show them a sample Safety Data Sheet (SDS), compared with the old MSDS
- Explain that the new SDS will not be available immediately, but will roll-out over a few years (or more)
*Please note the “Beer” hazard warning on the right is not GHS compliant.Â
For Help:
Mon 1 Apr 2013
So, while standing in the California jet-way waiting to board my plane, I noticed this sign. It was most likely a Proposition 65 labeling warning. However, what in the world do you do with that information? How did posting that sign change any behavior? Could I have done anything different to avoid the jet fumes?
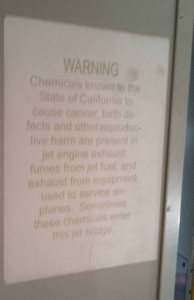
It reads, “Warning. Chemicals known to the State of California to cause cancer, birth defects and other reproductive harm are present in the jet engine exhaust fumes from jet fuel, and exhaust from equipment used to service airplanes. Sometimes these chemicals enter this jet bridge.”
In much the same way, sometimes our warning to employees is pointless. What can they do different? What is the point of telling them something if there is nothing we can do different?
The global harmonization system (GHS) is being implemented in the US by the end of 2013. By 2014 you must train your employees on the new changes to the (Material) Safety Data Sheets (SDS, now). (BTW, there are also some other things you must do).
The message I am trying to make (double irony, I know) is when you are training your employees, how do you measure the effectiveness If they “sign in and say they were in your training”, were you effective? Here are some suggestions, which might help to measure the right thing:
- Questions. This ___ number of the audience asked ___ questions.
- Feedback. I received ____ # of suggestions for the next training.
- Changes. They are going to implement ____ changes to their workplace.
- Secondary labeling. (GHS specific, of course) While walking around the site, I noticed ____ secondary labels with the new labeling pictographs.
I admit these aren’t the-best-suggestions-ever. But, warning someone without an alternative, method to change, or way to adopt a change, is really pointless.
Thu 24 Jan 2013
Posted by admin under industrial hygienist, Presentation, Training, Uncategorized
Comments Off on Educational opportunity
The Oregon GOSH (Govener’s Occupational Safety & Health) Conference is coming March 4-7, 2013. This is a great opportunity to get some information, education, and networking.
My suggestion is to attend the Tuesday and Wednesday sessions and cram-in as much as you are able. My break-out course is hidden well in the schedule, and will be easy to miss due to the other great sessions going at the same time. But, this is why I put a lot of my information on this website!
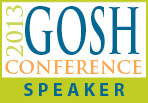
Hope to see you there.
Wed 21 Nov 2012
Posted by admin under Asbestos, Carcinogen, EPA, Federal OSHA, Hazard Communication, OSHA, Training, Uncategorized
Comments Off on What is disturbance of asbestos?
When training people who work around asbestos I usually discuss the word “disturbance” for a LONG time. The reason is simple. If you avoid “disturbing” it, you avoid most of the health issues.
As most people are aware, asbestos is found in many types of materials. Floor tiles, popcorn ceilings, wall panels, etc.
Disturbance relates to the specific activities you perform AND the type of material the asbestos is in.
If the asbestos containing material (ACM) is non-friable, then in theory, it takes more effort to disturb the asbestos. If the material is friable, well, you need to be REALLY careful. – and in some cases, breathing can disturb it. For example, an electrician who uncovers an ancient acoustical ceiling panel and finds damaged asbestos pipe insulation laying on top of it…is probably already in trouble. He has essentially disturbed friable asbestos by merely moving the panel.
In contrast, a remodeling company installing a floating laminate hardwood over asbestos 9×9 inch tiles (without damaging them) is [probably*] NOT causing airborne releases of asbestos.
Most of the OSHA/EPA asbestos rules hinge on the matrix of the material and the activity you are performing on it. The reason is this is what makes the asbestos fiber airborne.
*the OSHA rules are very specific as to work activity, please do your due diligence.
Tue 28 Aug 2012
Posted by admin under Asbestos, Federal OSHA, Hazard Communication, Management, OSHA, Training, Uncategorized
Comments Off on What makes it “hazardous”?
I love the show, “Dirty Jobs” with Mike Rowe. I find it fascinating what people are willing to do for work. Many of the jobs on the show have a true element of danger. Either a pinch point, an animal bite/kick, struck-by, heat/cold extreme, confined space, etc.
Did you ever consider what makes something hazardous?
My “deep thought for today” (thanks Jack Handy) is that education and training can make a job less hazardous. If you know how to do it right, and you know the risk, it doesn’t seem as dangerous anymore. The risk is there, but you know how to handle it, so the “hazard” seems to fade. This week I’ve given two separate asbestos classes to two different employers. At the beginning the employees were genuinely concerned about the hazards. By the end, they looked a lot more comfortable about upcoming project.
Is it any surprise that the HazCom standard is the most OSHA cited rule year over year?
So, keep up the training! Educate the employees on the dangers.
Mon 9 Jul 2012
Posted by admin under Asbestos, Lead, Management, Silica, Training
Comments Off on Construction Training Idea – add Silica
I was asked to perform asbestos training…and, “…maybe talk a little on lead”. However, I knew the employees needed to hear something totally different.
The firm requesting the training was a large excavation company that does a lot of road work. The training was at their bi monthly company wide meeting . I was given one hour.
So, my idea: Give them a quick overview of asbestos and lead, and then talk to them about silica. I called the training, “IH Health Topics in Construction”. And, as suspected, the questions that were posed all dealt with either: 1. “in my home I have…” or 2. silica and how to protect themselves.
I have made it my personal aim to talk about silica to as many employees as I can. I throw it into any training (even if I have just 5 minutes). Chances are, these guys WILL have overexposure to silica. Â The owner did not mind since I told him we were going to talk about a few different kinds of health issues in construction.
My suggestion: see if you can work Silica into your conversations and trainings.
Tags: construction, cristobalite, excavation, IH, quartz, safety, silica, silicosis, train, trained, training
Wed 16 May 2012
Posted by admin under Management, Mines, MSHA, Noise, Silica
Comments Off on MSHA Crushing Season
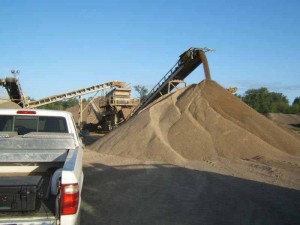
Here in the Northwest, rock crushing definately has a season…and that season is now. Road crews are getting set up and now is the time to make sure you get everything is in order…before the MSHA inspector shows up.
Below is my safety punch-list, specific to industrial hygiene:
- Training – I know it’s required for MSHA sites, but double check. Does everyone have it? What about contractors onsite?
- Water controls working & in place? The dust isn’t bad, yet.
- Air monitoring for silica – done it yet? Are you at a new location? New part of the quarry? Better do it again.
- Miner’s hearing checked (audiogram taken?). Anyone with a threshold shift? Make sure you follow up with another test.
- Are the air conditioning units working in the vehicles? – if they’re not= the windows will be down = noise levels WILL be up.
- Noise monitoring (dosimetry) performed 8-hour time weighted averages? If you don’t do it, MSHA will (maybe will be citation too).
- Is your shop done hardfacing the equipment? see my earlier post here.
- Paperwork in order?
Be safe out there!