Entries tagged with “safety”.
Did you find what you wanted?
Fri 6 Sep 2013
Posted by admin under Asbestos, Building Survey, Cadmium, Carcinogen, Exposure, Lead, Management, OSHA, Uncategorized
Comments Off on Let me give you a “hypothetical” worst-case scenario:
Hypothetically (and allegedly):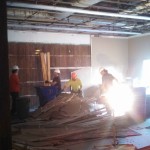
- You receive a project as a subcontractor.
- You are verbally told no asbestos or lead onsite. Only that’s not true.
- There is asbestos, and you, and multiple other subs, have disturbed it.
- The prime contractor says, “oops”. Has the materials tested, and then blames the owner for not letting them know.
- OSHA is called and citations are issued to the owner and GC for not testing and telling people.
- A year goes by and now both the owner and GC are being sued by 5 employees for $10,000,000 (yep $10 million, that’s the max BTW).
- As a footnote: this incidentally is not a worker compensation case (yet) since they are not suing their employer (they are suing the GC and owner)
Even if the employees don’t win $10m, are you prepared for: the headache, loss of client-relationship, trust breaking? Here’s a similar hypothetical article about such a situation.
On the flip side, here are some positive things you can do:
- get a written copy of the building survey (lead & asbestos) ALWAYS. (you might also ask for cadmium, radon, other possible hazardous substances)
- Train your employees about asbestos prior to having to deal with it.
- Give employees the power to “stop work” if they are suspicious of possible asbestos containing material (PACM).
- When handing out a building survey to your subs, get their acknowledgment (in writing, of course)
- Fight your OSHA citations. Go to your informal conference. Present your evidence and, at the very least, beg for forgiveness.
Mon 1 Apr 2013
So, while standing in the California jet-way waiting to board my plane, I noticed this sign. It was most likely a Proposition 65 labeling warning. However, what in the world do you do with that information? How did posting that sign change any behavior? Could I have done anything different to avoid the jet fumes?
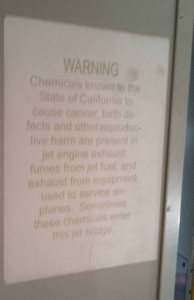
It reads, “Warning. Chemicals known to the State of California to cause cancer, birth defects and other reproductive harm are present in the jet engine exhaust fumes from jet fuel, and exhaust from equipment used to service airplanes. Sometimes these chemicals enter this jet bridge.”
In much the same way, sometimes our warning to employees is pointless. What can they do different? What is the point of telling them something if there is nothing we can do different?
The global harmonization system (GHS) is being implemented in the US by the end of 2013. By 2014 you must train your employees on the new changes to the (Material) Safety Data Sheets (SDS, now). (BTW, there are also some other things you must do).
The message I am trying to make (double irony, I know) is when you are training your employees, how do you measure the effectiveness If they “sign in and say they were in your training”, were you effective? Here are some suggestions, which might help to measure the right thing:
- Questions. This ___ number of the audience asked ___ questions.
- Feedback. I received ____ # of suggestions for the next training.
- Changes. They are going to implement ____ changes to their workplace.
- Secondary labeling. (GHS specific, of course) While walking around the site, I noticed ____ secondary labels with the new labeling pictographs.
I admit these aren’t the-best-suggestions-ever. But, warning someone without an alternative, method to change, or way to adopt a change, is really pointless.
Fri 1 Mar 2013
Posted by admin under Carcinogen, Exposure, Silica
Comments Off on Silica during chipping hammer
Yes, there can be airborne silica in the concrete when you are chipping up motar & tiles from a concrete base. This week a friend told me about his neighbor. He is a self-employed tile setter. He has worked in the industry for 20+ years. They just discovered he has cancer and will have the upper portion of his lungs removed.
Go here for more information. NPR article on silica rule delay.
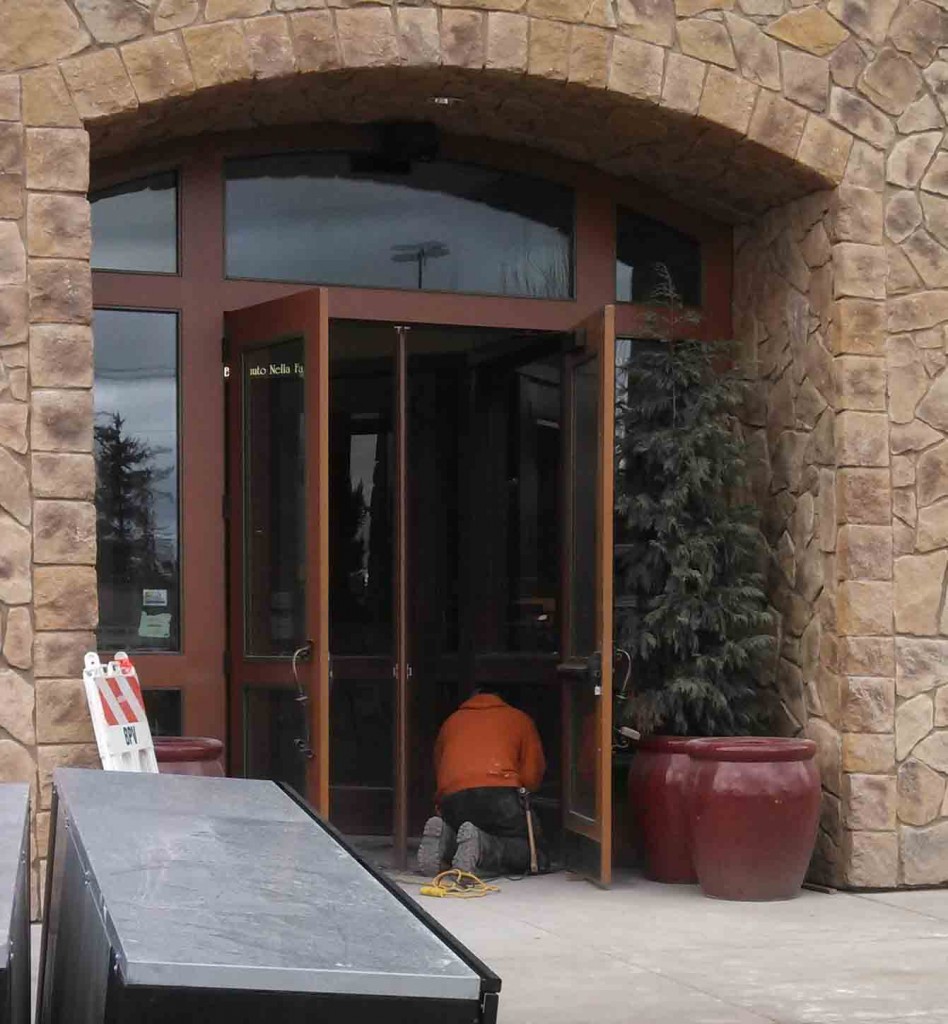
Fri 22 Feb 2013
Posted by admin under Admin Controls, Behavior Based, Fall Protection, Hazard Communication, Ladder, Ladders, Management, OSHA, Risk, Safety Policies, Safety Programs, Training
Comments Off on Focus on the biggest things first
Much research has been done in construction safety. If you are working in construction, you have probably heard the facts over and over. The majority of construction injuries are from four main hazards, hence the “focus four hazards“. Although this site is for health issues & industrial hygiene in construction, it would be ridiculous to NOT mention these other hazards.
- Falls,
- Caught-in or Caught-between,
- Struck-by &
- Electrocution.
When talking with superintendents and safety coordinators, you can usually tell very quickly  if they have these under control. Either their subcontractors already do it right, or if/when they see an error, they immediately stop and address the inefficiency.
I saw this ladder in front of my children’s school. There was no one around and, by the look of it, there might have been someone on the roof. I should have waited, or fixed the ladder and spoken to the individual. But, I didn’t. Instead, I took a picture, put it on the internet, and now I’m telling everyone why it’s wrong.
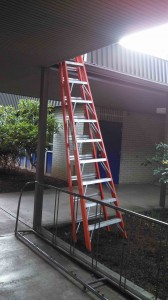
Wed 13 Feb 2013
Posted by admin under Chlorinated Solvent, confined space, Engineering Controls, Galvanized welding, Hexavalent chromium, Noise, Personal Protective Equip (PPE), Respirators, Risk, Stainless Steel, ventilation, Welding
Comments Off on Welding health & safety
I’m easily impressed with welding and welders. Welding looks so simple, yet hard, dangerous and permanent.
When interviewing your welder, here are some questions to ask: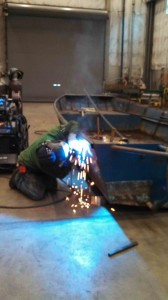
- What type of welding are you doing?
- What type of metal do you weld on? (mild steel, stainless, galvanized)
- Is there any coating on the metal?
- What type of flux is used?
- Where do you weld?, and then, “Where else?”
- Is there any ventilation in the area you weld?
- Are there any flammables in the area?
- Do you wear any PPE when welding? (ear plugs, respirator, leather)
- When do you use fall protection?
- Do you have & use welding shields?
What makes welding so difficult is the number of variables involved. The welding variables can change by the minute. Educate your employees on these dangers.
After the above questions, if the employee is agreeable, I ask some additional questions. These are the ones that provoke the best stories:
- What is the strangest things you’ve welded?
- Have you ever welding in a really small (confined) area?
- Have you ever welded with exotic metals? fluxes?
- What’s the worst thing you’ve welded on?
- Have you ever gotten sick from welding?
There are many, many more questions to be asked depending on the answers. The authority on this subject, Michael Harris, has written an excellent book on this subject, “Welding Health and Safety“(ISBN 978-1-931504-28-7). It is available from AIHA. It is VERY detailed, and money well spent if you do welding. I have taken his short course (all day) and I learned more than I ever thought possible, and I still can’t even weld!

Thu 24 Jan 2013
Posted by admin under industrial hygienist, Presentation, Training, Uncategorized
Comments Off on Educational opportunity
The Oregon GOSH (Govener’s Occupational Safety & Health) Conference is coming March 4-7, 2013. This is a great opportunity to get some information, education, and networking.
My suggestion is to attend the Tuesday and Wednesday sessions and cram-in as much as you are able. My break-out course is hidden well in the schedule, and will be easy to miss due to the other great sessions going at the same time. But, this is why I put a lot of my information on this website!
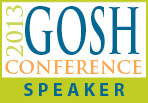
Hope to see you there.
Fri 14 Dec 2012
Posted by admin under Air Monitoring, Chemical Exposure, Engineering Controls, Hazard Communication, industrial hygienist, Management, Multi gas meter, odor thresholds, Risk, Safety Policies, Safety Programs, Training
Comments Off on Multi gas meters (4-gas)
Many construction companies have a multi gas meter (s). Here is my word of caution: if you have one, know how to use it.
I bet if you’re reading this post, you do know how. However, do your employees?
This type of training is SO critical. Below are some common mistakes I’ve seen from construction companies using these types of equipment:
- Let someone else (a GC, or subcontractor) tell you if it’s ok to enter a confined space (or hazardous one).
- = do you own monitoring, & use your own equipment!
- Use someone else’s multi gas meter.
- =do NOT use someone’s meter unless you 1. know the machine and 2. are able to calibrate and see the documentation. Would you send your employees to work in an area you think there might be a deadly hazard? Treat the 4-gas meter like it is your only available tool.
- Not performing a precalibration and bump test before using the gas meter.
- = ALWAYS perform a bump test (not just zero-out)
- Not knowing which sensors are inside the machine (and what they mean).
- =train your employees on when/why it alarms. CO is not CO2.
- Blame the machine if it alarms
- =the machine is alarming for a reason. You either screwed it up, or something is going on. Figure it out. I had a project where the handheld radios were interfering with the multi gas meter. It took us 2 days to figure this out. Luckily no one was so desperate to work they ignored the alarm. On another project, employees were telling me it was ok to work while the alarm was sounding off. Their response was that, “it always goes off for CO, but we aren’t worried”. Yikes! I was.
- Not knowing what the hazards are
- =you must know what you are measuring for. If you have isocyanates inside the confined space, the multi gas meter is probably not going to give you adequate warning.- if any. Just like wearing the right type of filter cartridge on your respirator, know the hazard you are measuring.
Wed 12 Dec 2012
Posted by admin under Air Monitoring, Behavior Based, Concrete, Dust, Engineering Controls, Exposure, Hazard Communication, HEPA, Management, Personal Protective Equip (PPE), Respirators, Safety Policies, Safety Programs, Silica, Training
Comments Off on Pre task planning – for silica
Controlling most of these types of exposures is really simple. If you know the job- and you know it will generate airborne silica = Pre Task Plan!
I wish Superintendents would enforce their project managers, or project engineers, to make a pre-task plan for every concrete/silica producing task. Then, (please don’t stop yet), review the plan once the project starts!
Below are two examples with different outcomes: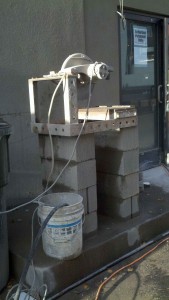
1. Cutting concrete block.
The pretask plan called for a garden hose with attachment(s) to wet the cutting area. Everything was perfect until the water was shut off. But, they improvised and found an electric water pump with bucket and recycled the water. It was a great outcome. What if the power went out? They could have used a Hudson sprayer.
2. Grinding plaster off a brick wall.
They built an enclosure and containment. They had a negative air machine with HEPA filters. They had a vacuum with HEPA filters, tyvek, 1/2 face respirator, eye protection, etc. But, as they worked the vacuum couldn’t keep up with the amount of dust generated by the 7 inch Bosch grinder. It was really dusty. They worked like this for days. No one onsite saw them because they were in containment. Unfortunately the project is almost over and it could have been better. A simple shroud to the grinder, like this one (no endorcement) might have controlled the dust & silica. Sure, it might have been troublesome to find the exact one, and get a vacuum attachment, and have the extra weight, and ….
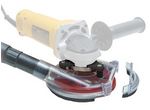
So, let’s talk to people about silica, talk about solutions, and then check to see if they’re effective.
Thu 6 Dec 2012
My friend, Shelley, sent me these pictures of a city maintenance crew hanging up the Christmas decorations in town. These guys have probably been working this way for years. What will take to make them change? Administrative controls? As I’ve mentioned before, falls are the #1 killer in construction.
 
Mon 3 Dec 2012
Posted by admin under ACGIH, Federal OSHA, GHS, industrial hygienist, Management, Misc, MSDS, OSHA, PEL (Perm Exp Limit), Risk, SDS
Comments Off on Why I’m excited about the new GHS rules
The new global harmonization system (GHS) is officially adopted by OSHA. Each state run program is rolling out their acceptance of the new changes. Where I live, we have until December 2013 to train employees in this new type of hazard communication.
Honestly, I’m NOT too EXCITED about it. But, I’m trying to have a good attitude. Below are some good things which may occur:
- Raise the level of awareness of hazardous materials & their toxicity
- Train employees (hopefully, retrain) on how to handle chemicals
- More training = less citations. (?)Â OSHA’s top ten citations include #3 – hazard communication. Maybe people will actually do the training?! (my guess is that there will be more citations)
- Consistent information worldwide. Â All UN countries should have the same format. (this might take years)
- Proprietary information will be more visible on the SDS. In the new rules, manufacturers are required to list the % of their proprietary ingredients.
- Pictograms! They’re so cool. My favorite is the exploding person.
- Maybe this is my favorite?!: Manufacturers will have to look again at their products and classify them according to the physical & health criteria. Nowadays with more relevant information from worldwide occupational exposure limits, it might help make employers aware of the hazards.
- This might help OSHA enforce newer exposure limits (other than the 1978 AGCIH TLVs).
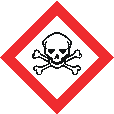
How do you plan on training your employees? If you need help, contact me here.