Entries tagged with “IH”.
Did you find what you wanted?
Thu 4 Dec 2014
Posted by admin under Air Monitoring, Asbestos, Building Survey, Carbon Monoxide, Concrete, Dust, IAQ, industrial hygienist, occupational hygiene, Presentation, Silica, Training, Uncategorized
Comments Off on All I want for my (IH) Christmas…
Here’s my top 5 gifts for Christmas in the (my) occupational hygiene world of construction:
- A new carbon monoxide monitor.
- Not just a “normal” $40 model. A Nest Protect Fire & Carbon Monoxide monitor, which is in the $100 range. This thing is sweet. Talks to you, sends you a text message. Here’s a review from Cool Tools. Or, just buy it here.
- High flow air pump, Gast model.
- I have some other flow rate pumps up to 5 liters per minute (LPM), but this one is great for flow rates 10-up to 28 LPM (depending on the model). Good for high volume area type samples and vacuum wipe sampling. You must have 110 power available, but once calibrated, it’s a done-deal. They can be bought for under $250. Grab a rotometer too, if you don’t have one.

- Wireless response system to use during training.
- Attendees have a wireless response keypad and the trainer can ask a multiple choice question. It allows the audience to reply. The results then show up on the screen. Great for anonymous responses, or a general overview from your audience. There are several vendors, here’s an example, and the leader in the industry is Turning Point. I think these are in the $500-$1,000 range.
- A bulk asbestos example kit.
- A bunch of “typical” building materials which are asbestos containing. In sealed glass jars, of course. I don’t know where you’d buy this sort of thing. I wish I would have kept all of my samples over the years.
- A dedicated short term silica sampling kit.
- SKC has a new sampler which can sample at a higher flow rate  of 8 LPM, compared with the usual 2.5, or 1.8 LPM. (which, if you think through the math; allows you to achieve a detection limit with a lower sample volume, and a shorter time duration) Unfortunately, you must purchase a new SKC Leland pump/charger, PPI sampler, calibration junk. Total cost is probably in the $2,000 range.
Wed 26 Jun 2013
Posted by admin under Air Monitoring, Building Survey, EPA, Exposure, IAQ, industrial hygienist, Management, NIOSH, occupational hygiene, PCB, Risk, Uncategorized
Comments Off on PCBs in caulk
Yep. Polychlorobiphenyls (PCB) are found in caulking. Typically buildings before 1979 have this caulk. (EPA Facts about PCB in Caulk) The only way to know is to test. BUT, wait!
Either:
- Assume you have it and renovate with caution. Or,
- Have the air tested for PCBs in the air.
Do not have a bulk sample taken. You should ask for an exposure assessment to be performed (air monitoring) by a qualified industrial hygienist. The reason is two-fold.
- The potential for the hazard is airborne. In most instances, people aren’t getting exposure from any other method.
- By measuring the air, you account for any other sources of PCBs (paint, ballasts, oils, ceiling tiles).
Most of this caulk is found in outdoor uses (high grade) in older buildings up to around 1980-ish. If an airborne exposure assessment finds levels below the acceptable rules & recommendations (depends on age & location), you may continue with your project. Of course, you would take appropriate precautions, like these recommendations from the EPA. They also have a very nice flow chart. Just like a choose-your-adventure book, make sure you don’t fall into the “Abatement” box!
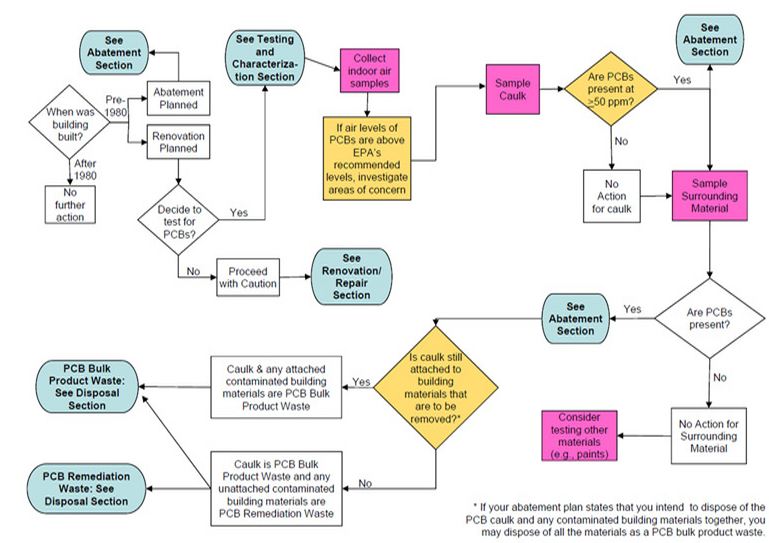
Tue 12 Mar 2013
I had the opportunity to attend a construction safety award presentation and listen to various commercial construction companies (GC, and Specialty Contractors) explain why their company deserved an award. Owners, CEOs, Safety Directors, and Employees spoke about their company. Their stories were amazing. Below I have listed some of the ideas that inspired me. They may not, at first glace, appear to be amazing. However, consider when the CEO tells a story that makes him cry, or when a superintendent explains how he is part of a family,…. it makes the words ring different.
Here are my takeaways:
- Safety really starts at the top. It’s not a priority, it’s a core value. Check out the Injury Free Forum (IIF).
- This is basically a club/meeting for CEOs to gather and talk about how to prevent injuries. It’s ‘almost’ an invite-only type of event. But, if you’re a CEO/President you should think about it. (helps if you live in the NE part of the US)
- Here are some companies participating, Gilbane, Gilbane video (yep, it’s good), JMJ Associates, Baker Concrete video
- During initial employee orientation;
- one company has each employee write a letter to their family saying (apologizing) why they are gone/dead. This really emphasizes to each individual why they need to work safe.
- the CEO gives each new employee his business card and tell them to call him directly if they are asked to do something unsafe.
- each new employee is assigned a mentor (the time period varies from 2 weeks to 1 month) to watch them work safely.
- Each employee has the right to stop work due to safety. If they do it: the CEO/President writes them a personal thank you note.
- Make each near miss a incident, but do NOT have a lot of paperwork, just simple documentation for future learning.
- Have a innovative idea challenge at your company for good safety ideas.
- Put a bar code on infrequently used tools. Link to a short video which explains how to use it.
- Zip tie PPE onto the tools upon checkout.
- Send your “Safety Incident” or “Safety Summary” to their home. Ask them to put it on their fridge. Then, run a contest. Randomly find a name & call that employee to see if they can tell you what the safety topic is. Give a prize. Repeat.
- Look at the design. A large GC mandated that every hole in their project have safety netting installed during the concrete pour. …and they did it!
- An electrical firm uses no knives. None. Think that helps cut down on injuries? (pun intended)
The goal is zero injuries. So, what happens after zero injuries? How about sending your spouse to work…and they come home healthier! It’s not far away for some companies, Health & Wellness programs are already being implemented. For whom are you working? Here’s one of my reasons:
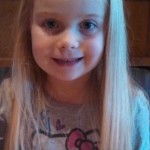
Wed 17 Oct 2012
Posted by admin under Admin Controls, Air Monitoring, Concrete, confined space, Engineering Controls, Exposure, Federal OSHA, fit testing, Hazard Communication, Hearing Conservation, hearing protection, Management, Noise, OSHA, Permit Required, Personal Protective Equip (PPE), Respirators, Safety Policies, Safety Programs, Silica, Training, Uncategorized, ventilation
Comments Off on Ready Mix Drum Chipping
If you operate a ready-mix plant and have concrete trucks, you are aware of this process. Once a year (hopefully, only once) a person must climb into the drum of the ready-mix truck and chip off excess concrete. What happen during regular use, is that some concrete hardens, which usually sets-up over and around the blades. Access into the drum is by either the 3×4 hole in the side, or down the chute.
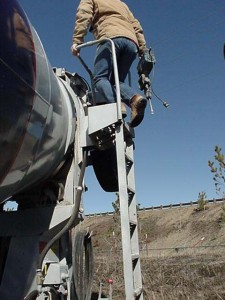
Yes, it is a confined space (def’n: 1. large enough to enter, 2. not designed for occupancy, and 3. limited entry/egress).
Here are a list of the possible hazards:
- silica dust (from chipping concrete)
- noise exposure
- hazardous atmosphere (curing concrete uses up oxygen, which we DO need BTW)
- slipping hazard (drum is round inside)
- heat stress (if you’re trying to do this activity in the summer)
- eye hazard (chipping)
- electrical hazard (if you’re using water & have an electric hammer)
- lock out / tag out (if the truck drives away, or if the barrel starts turning)
There are many resources available (see below). Some things to keep in mind; ventilation (fans, etc) to control the airborne silica dust are usually not effective (too much dust versus exhaust). Water controls are best, but you must limit the amount of water and the direction of the sprayer. I suggest looking at what others have done.
Keep in mind, if you perform this activity you will need (as a company):
- respiratory program (medical, fit test, written plan)
- confined space program (multi gas meter, written program, attendant?)
- lock out /tag out policy or procedures
- training (for each of the above, and for this specific activity)
At this point I know what my contractor-friends are thinking…I will subcontract this out!  ha. If you do, please make sure your sub is doing it right.
Resources:
Georgia Tech – good presentation & guidance
Georgia Tech/OSHA – Safe Work Practices (in Spanish too!)
Teamsters H&S hazards & controls
Illinois DCEO – Consultation on ready mix cleaning
Thu 16 Aug 2012
Posted by admin under Air Monitoring, Cadmium, Concrete, Drywall, Dust, Exposure, Hexavalent chromium, industrial hygienist, Lead, Management, Mold, Silica, TWA, Welding
1 Comment
When performing air monitoring it can be useful to take multiple samples on the same individual throughout the day. Here are some reasons to change out the filters:
- build up of dust on filter – can cause overloading
- break-out the exposure data. Morning versus afternoon, or by job tasks, or the physical area the employee is working in, controls vs. no-controls, etc.
- if you question the employees motives. If you think the employee might skew the results, multiple samples might give you better control- or at least tell you if one is way-out-of-line.
Once you have your data results, how do you combine them?
If you’re taking particulate (dust, lead, cadmium, silica, etc) and you have the concentrations (from the lab) here is what to do.
- note the time (in minutes!) and the concentration results (mg/m3, ug/m3, etc) for each sample
- multiply the time and concentration for each – then add each number together
- finally, divide the above number by the total number of minutes sampled. This is your time weighted average (TWA).
Simple?! Yes. …And it’s really easy to make a mistake too. Check your math, and then eyeball the results and see if they make sense logically.
Here’s an example:
Andrew took three samples during one shift while Shelley was rivet busting through leaded paint. The first sample (118 minutes) was reported as 6.8 ug/m3 of lead, the second was for 245 minutes and had a concentration of 18 ug/m3. The last sample was taken for 88 minutes and was reported a level of 29 ug/m3. The overall results is 17.2 ug/m3 for the total time sampled. (Side: if you sampled for their entire exposure, and they worked longer hours, you could add those hours (assuming zero exposure) into the final time-in step three)
See the math below:
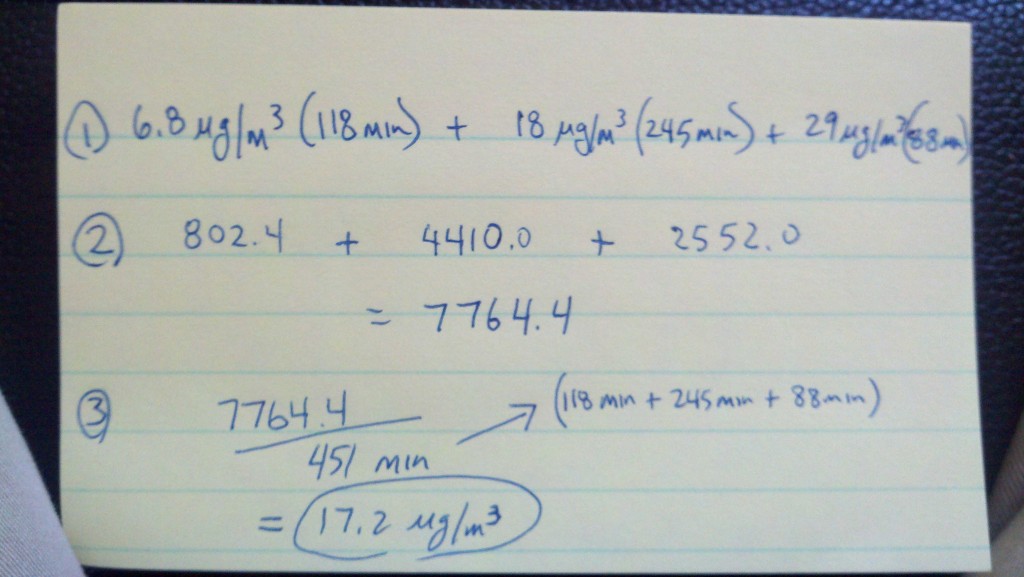
Wed 25 Jul 2012
As I have said in an earlier post, some OSHA, EPA, and MSHA rules are a good fit. They blend well with health research, scientific technology, good practices, and a low-cost-of-compliance for employers. Other rules are just bad. They are  totally out of date, not protective enough, or just not feasible/practical. Here’s my plug for a good safety manager/industrial hygienist – A good one will know which rules/guidelines to follow.
The New York Times (July 19, 2012, Cara Buckley) recently wrote an article on the US noise standards which are not protective enough for employees. In construction we also have three additional problems.
- hearing loss is expected (or at least assumed in certain fields – carpenters, sheetmetal, ironworkers, etc.) and,
- work shifts are usually over 8-hours. Noise exposure is usually calculated on an 8-hour time weighted average. During the busy months, an 8-hour work day is rare. It’s at least 10, maybe 12-14 hours. This doesn’t allow your ears to “rest” between shifts. For more information on extended work shifts go here.
- extracurricular activities contribute to overall hearing loss – my point is that most construction workers don’t sit at home at the end of their shift. Almost everyone I know in construction is involved in one of these activities: hunting, shooting, motorcycles, water sports, yard work, cars, wood working/cutting, concerts, music, etc. Each of these activities contribute to their overall hearing loss, and again, doesn’t allow your ears to “rest”.
…which reminds me that I need to keep a set of ear plugs in my motorcycle jacket.
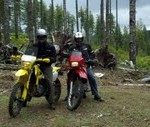
Tags: ACGIH, dBA, dosimeters, EPA, hearing loss, IH, noise, OSHA, safety, sound, sound level, standards, TWA
Fri 20 Jul 2012
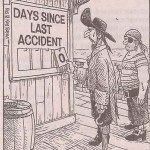
Are you measuring for zero accidents? Is this even possible? I agree it is a worthy goal. But, if you are presenting this to management, can you actually achieve it?
There is plenty of discussion around this issue. Maybe a better goal is something harder to measure, but more successful/beneficial in the long term. What about measuring one of these? (or a combination)
- response time from complaint to resolution (from employees)
- number of requests for safety related issues
- satisfaction of safety by workers (rate 1-10)
- safety committee interest & interaction
- decrease in airborne exposure levels year over year
- keeping track of engineering/administrative controls put in place per year
My 2 cents.
Wed 18 Jul 2012
Posted by admin under Air Monitoring, Asbestos, Building Survey, Hazard Communication, Management
Comments Off on What if you’ve had asbestos exposure?
Occasionally (actually, far too often), I hear from a subcontractor who was told by the General Contractor (or owner) there is no asbestos onsite. Then, after they have been working for a month they find out it actually IS asbestos, and they were disturbing it. What do you do?
The first thing to do is stop work. Do not try to clean it up. Call an abatement contractor. They will identify the asbestos onsite, clean it up, and provide an airborne clearance test.
Next, you will need to provide awareness training (or better, let the abatement company provide it). Ideally this will occur on the day you start back working. Train everyone onsite about asbestos.
Finally, you (as the safety manager), need to identify and characterize the exposure to the employees. It should probably be a formal letter written to the owner, general contractor and employees.
Here are some tips on writing the letter:
- include employee names, work hours, type of work, PPE worn, and locations they were working
- describe the asbestos. Amount found, locations, type, estimated amount disturbed.
- describe remedy process and steps taken. Names of GC, owner, abatement company, airborne levels found. Who was trained afterwards.
- describe how things will change in the future. Here’s a tip: Â any building before 1985 WILL have a building survey performed for asbestos….in writing.
Really, one exposure to asbestos is probably* not enough to contract a disease (asbestosis, or mesothelioma). It will take 15-30 years for symptoms to appear. But, it might be worth the “goodwill” to send affected employees into a occupational health doctor for a check up. The physician will reassure the employee and may provide some comfort.
*asbestos is a carcinogen. Greater exposure = greater chance of cancer. no amount is safe.
Mon 16 Jul 2012
Posted by admin under fit testing, Respirators, Safety Programs, Training
Comments Off on Fit Testing – tips and suggestions
There are two types of fit testing, 1. quantitative and, 2. qualitative. For quantitative fit testing you’ll need a machine (ex. Portacount), Â a respirator that will protect more than 50x the limits (>full face). Â I will not cover this type of fit testing in this post, but it is very similar.
For qualitative fit testing you will need:
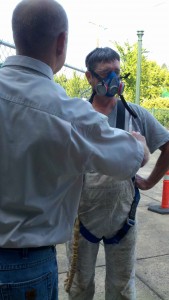
A medical clearance (not needed if you are wearing a paper dust mask) for each employee wearing a respirator.
Respirator w/P-100 filters (1/2 face respirator or more protective), aka HEPA filters, purple in color.
fit test kit -your choices are: saccharine, irritant smoke, Bitrex, or isoamyl acetate-bananas. Buy it online, or at your local safety supplier. Look at their instructions.
My preference is to use irritant smoke. The reasons are;
- Â if they cough, it means they smelled it.
- it doesn’t require a containment to be built to perform the fit testing.
The employee must be clean shaven around where the mask touches the face. Â I allow “short” goaties where the facial hair does not touch the mask. The fit test procedures are easy to follow and found inside the kit. There are 8-steps, do each one for about 1 minute each.
As you fill out each individual’s form, make sure you include:
- if the employee is clean shaven
- what type of respirator is being worn (size, brand, model)
- what type of filters are being worn
- what type of fit test kit you used
While you have the employee captive, you might as well give them some training. Here are some questions and/or points to note.
- did you train them on positive & negative fit checks?
- why are they wearing a respirator?
- what are the limitations of their respirator?
- how will they store the respirator?
- how will they sanitize it?
- will they share their respirator?
Finally, sign and date the form. It expires one year from this date. Simple? yes. Â Easy to forget something? yes.
Tags: fit check, fit test, fit testing, IH, industrial hygiene, qualitative, quantitative, respirator, respirators, safety, train the trainer
Mon 9 Jul 2012
Posted by admin under Asbestos, Lead, Management, Silica, Training
Comments Off on Construction Training Idea – add Silica
I was asked to perform asbestos training…and, “…maybe talk a little on lead”. However, I knew the employees needed to hear something totally different.
The firm requesting the training was a large excavation company that does a lot of road work. The training was at their bi monthly company wide meeting . I was given one hour.
So, my idea: Give them a quick overview of asbestos and lead, and then talk to them about silica. I called the training, “IH Health Topics in Construction”. And, as suspected, the questions that were posed all dealt with either: 1. “in my home I have…” or 2. silica and how to protect themselves.
I have made it my personal aim to talk about silica to as many employees as I can. I throw it into any training (even if I have just 5 minutes). Chances are, these guys WILL have overexposure to silica. Â The owner did not mind since I told him we were going to talk about a few different kinds of health issues in construction.
My suggestion: see if you can work Silica into your conversations and trainings.
Tags: construction, cristobalite, excavation, IH, quartz, safety, silica, silicosis, train, trained, training