Posted by admin under fit testing, Respirators, Safety Programs, Training
Comments Off on Fit Testing – tips and suggestions
There are two types of fit testing, 1. quantitative and, 2. qualitative. For quantitative fit testing you’ll need a machine (ex. Portacount), Â a respirator that will protect more than 50x the limits (>full face). Â I will not cover this type of fit testing in this post, but it is very similar.
For qualitative fit testing you will need:
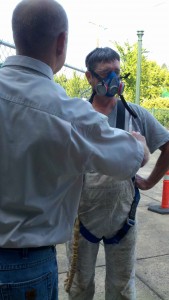
A medical clearance (not needed if you are wearing a paper dust mask) for each employee wearing a respirator.
Respirator w/P-100 filters (1/2 face respirator or more protective), aka HEPA filters, purple in color.
fit test kit -your choices are: saccharine, irritant smoke, Bitrex, or isoamyl acetate-bananas. Buy it online, or at your local safety supplier. Look at their instructions.
My preference is to use irritant smoke. The reasons are;
- Â if they cough, it means they smelled it.
- it doesn’t require a containment to be built to perform the fit testing.
The employee must be clean shaven around where the mask touches the face. Â I allow “short” goaties where the facial hair does not touch the mask. The fit test procedures are easy to follow and found inside the kit. There are 8-steps, do each one for about 1 minute each.
As you fill out each individual’s form, make sure you include:
- if the employee is clean shaven
- what type of respirator is being worn (size, brand, model)
- what type of filters are being worn
- what type of fit test kit you used
While you have the employee captive, you might as well give them some training. Here are some questions and/or points to note.
- did you train them on positive & negative fit checks?
- why are they wearing a respirator?
- what are the limitations of their respirator?
- how will they store the respirator?
- how will they sanitize it?
- will they share their respirator?
Finally, sign and date the form. It expires one year from this date. Simple? yes. Â Easy to forget something? yes.
Tags: fit check, fit test, fit testing, IH, industrial hygiene, qualitative, quantitative, respirator, respirators, safety, train the trainer