As the saying goes, “if I had a penny for every time someone asked me…” Well, here are my most commonly (frequently) asked questions (FAQs) for dealing with asbestos and lead on a construction job-site. These are my answers, so consult the appropriate governing body.
LEAD
- Do I need to comply with EPA’s new lead rule? How do I?
If you are working in a public area, or specifically, with kids under the age of 6, you MUST comply. Go to EPA’s website (www.epa.gov) and take an accredited training class and get your company approved for leaded paint activities.
- How do I know if I have leaded paint on my job-site?
If the building was built before 1978, a building survey (performed by an accredited inspector) should be taken. Rumor has it that leaded paint can be found in buildings up to 1985 or later. An accredited inspector can be found by calling the Construction Contractors Board, OSHA, or the EPA/DEQ.
- Can I use a do-it-yourself lead testing kit?

Yes, but they can sometimes be misleading. They only test the surface paint -not the other layers below. In addition, these kits cannot determine the amount of lead, or the airborne levels of lead on your jobsite.
- I do have leaded paint on my construction project. Where can I find the current regulations on how to handle this situation?
OSHA (www.osha.gov), the Environmental Protection Agency (EPA) aka: Department of Environmental Quality (DEQ), the Construction Contractors Board (CCB), and sometimes Department of Human Services (DHS). Many of their rules overlap, but they all have unique rules that are designed for their particular jurisdiction.
- We had a building survey for lead hazards performed. Our accredited inspector had the paint tested and found that it was only 0.3% total lead. It is less than 1%, do we need to comply with the regulations since it is such a small amount?
Yes. Any amount of lead found in lead paint requires that comply with OSHA’s regulations. Depending on the project, you may also need to comply with the standards of other governing bodies (see above).
ASBESTOS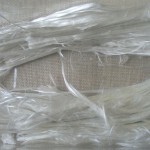
- How do I know if I have asbestos on my jobsite?
Buildings built before 1980 are required by DEQ to have a survey performed before any demolition or renovation. The survey must be performed by an Asbestos Hazard Emergency Response Act (AHERA) accredited inspector. They will take bulk samples of the material and determine the amount of asbestos present.
- The accredited laboratory reported the asbestos had less than 1% but more than 0.001%. Does this mean it has asbestos?
Yes, it has asbestos (less than 1%), but OSHA considers it to be non-asbestos containing. However, even at 1% asbestos, you would want to control the possible exposures. Work practice procedures, training, and PPE should be used.
- There is a small quantity (less than 10 linear feet) of asbestos on my jobsite. My employees may have to touch it. What type of training do they need?
There are four classes (or types) of asbestos work. Class I is the most hazardous and Class IV is the least hazardous. To answer your question-you need to compare your situation to the definition of Class III and Class IV asbestos work. Class III work is defined as, “repair and maintenance operations, where asbestos containing material, including thermal system insulation and surfacing asbestos containing material is likely to be disturbedâ€. This type of training is 16 hours in length and must be done by a EPA/DEQ certified trainer. Class IV work is defined as, “maintenance and custodial activities during which employees contact but do not disturb asbestos containing materials and activities to clean up dust, waste and debris resulting from Class I, II and III activitiesâ€. This type of training is 2 hours in length and is the minimum. The particular type of training needed will depend on your situation.
- We obtained a building survey before starting our job-site. After we started demolition we found some “questionable building materials†that did not look like they had been tested in this report. What do I do?
Stop work. Call an accredited building inspector for the material you need to test and have the material tested. Then report the results to the owner, and others on the jobsite, within 24 hours.
- Our company policy is that we do not touch asbestos or lead. Do I need to write that down as “my company policy�
Yes. Plus you should include what your employees should do if they run across a “questionable†material and whom they should contact.
- We subcontract all asbestos and lead work. Do I need to have my employees trained in lead and asbestos awareness?
Yes. There is still a good chance that your employees will see or have to deal with these hazards on the jobsite.