I was asked to summarize my thoughts on the OSHA proposed silica rule (which is currently pending). I’ve done it before, but since it was for the ASSE’s Industrial Hygiene Practice Specialty, it seemed fitting to post it on this site as well.
Wondering what is happening with the OSHA crystalline silica rule? In aviation terms it’s called a holding pattern. This airplane may-or may not-land. And, it is anyone’s guess.
If you haven’t heard, Federal OSHA is proposing to reduce the airborne silica permissible exposure limit (PEL) to 50 µg/m³. It is difficult to say how much lower this new rule will be, since the current standard relies on a calculated formula to obtain the exposure limit. However, for rounding purposes, let’s just say it’s a 50% reduction in the PEL. This limit is the same at the NIOSH Recommended Limit but still above the ACGIH (2006) Threshold Limit Value of 25 µg/m³.
Over the last year my views on this rule haven’t changed much: It’s a mixed-bag. There are still overexposures to silica. However, will the new rule change behavior?
To show some of the contrast, let me explain. Overexposures to airborne crystalline silica are still occurring. However, silica deaths have continued to decrease over the recent past (without the new rule). But, will the small employers comply? Or just wait to be cited? There is rarely a perfect solution for all situations. I’d like to provide a perspective balance to both sides of the rule.
Benefits:
The obvious benefit to lowering the silica exposure limit will be to protect overexposures to silica. I believe the rule will accomplish this in a number of ways. Any new rule will generate increased awareness for the subject of silica. The new rule will drive OSHA compliance by both lowering the PEL and by compliance with their additional controls. This will drive changes and modification to industries. Innovation will be spurned for controls and the need to comply. Â In turn, this will create more discussions on the topic, the solutions, and overall awareness.
The new rule will get closer to the ACGIH TLV and update the health standards. The original rule was from the 1970s. And, OSHA is on the prowl for ways to update their current PELs.
Health and safety consultants will have an occasion for additional revenue in training, air monitoring, recommending controls, and other opportunities.
The new rule allows for alternatives to sampling. Rather than air sampling, you can choose to “over protect” and assure employees are controlling silica exposures. This is a great solution for short duration tasks where exposure monitoring is prohibitive (see Table 1 from OSHA’s Fact Sheet). They emphasize control measures for silica.
There are very few new products and control measures for mitigating silica exposure in industry. Technology has somewhat sidestepped innovating products for dust capture and control for concrete work. Hopefully new products will be created to control silica. If nothing else, maybe we will see frequent job safety analysis (JSA, JHA) as a common practice to control exposures.
Weakness:
However, there are notable weaknesses to the proposed rule. The obvious downside is employers are expected to spend money. This will be an additional cost to doing business. Money will be spent on citations, controls for silica, labor during the activities, and for consultants to verify exposures are below the PEL.
This new rule will also allow OSHA to issue citations easier. There are many items in the new rule which are beyond merely lowering the exposure limit. I imagine compliance officers will cite for failure to implement controls, or other technical aspects, rather than measuring the airborne dust and finding overexposure. Look for more drive-by citations.
And, there will be more confusion. Remember explaining to people how to calculate the current PEL? Well, in the short term, it won’t get easier. Although the PEL will be a fixed amount, there will be other things to explain. And, remember all the OSHA rules for leaded paint? The new rule is similar in how it allows you to provide adequate PPE and controls for “interim†work without measuring airborne levels.  Imagine you are a smaller contractor employer. This will be confusing and a lot of background work in order to use a jackhammer for one small project.
And, analytically, the airborne levels attempting to be achieved are so low, they are at the laboratory detection limits. With laboratory I currently use, to reach the detectable minimum PEL you will need to sample for at least 80 minutes (200 Liters). There is some newer sampling equipment which makes these levels easier to achieve. But, guess what? That will cost more money. In addition, contained in the rule are mention of specific medical evaluations and facilities for those with continued overexposures. There are not enough medical facilities to support the number of people who need them.
Summary:
Overall, I believe the new silica rules will help reduce overexposures to silica. The increase in awareness across the US will bring more attention to the danger. Employers who are doing absolutely nothing to control silica will get caught, punished, and hopefully change their ways. For employers already in compliance, there will be a small, but manageable, learning curve. I also see many contractors using interim controls (Table 1) as a guide to easily protect employees on short tasks with high silica exposures.
To stay ahead of the curve, the AIHA has released (2013) a white paper for guidelines on skills & competencies in silica specific to construction. It is a great outline for training your employees. Another great resource for awareness and silica control measures is silica-safe.org. As a reminder, pre-task planning is still one of the best methods for health and safety.
 Here’s my sampling outfit.
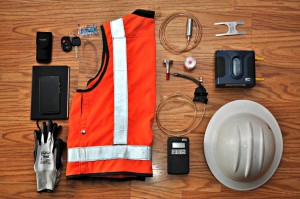