I’ve had some good questions come out of the silica training sessions I’ve given in the past year. Below are some of the better ones.
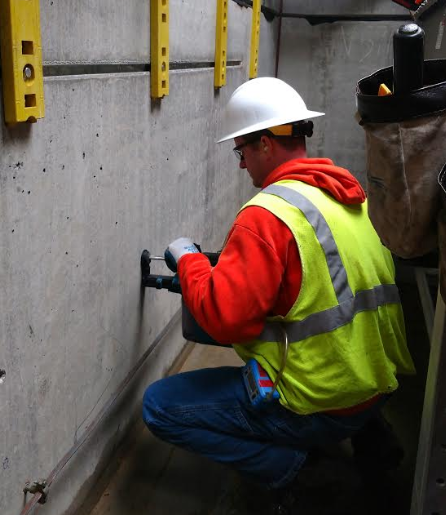
- How often do we need to perform competent person training?
- There is NOT a specific answer to this question. But, OSHA considers this as a performance standard, so if employees are not performing their “competent person” duties, then you must retrain. I personally think this will vary depending on how often they are engaged in these types of activities, the size of the company and how often you discover gaps. I’ll guess and say every 1-3 years.
- How do you dispose of silica dust, after it is collected in a 99% efficient vacuum?
- OSHA says not to reintroduce this material into the air.
- I have explained in classes that if you learn about particulate capture technology, you’ll see that the small (less than 5 micron) size are captured by electrostatically attaching to a larger particle. So, if you are collecting these particulates in a vacuum, they should be attached as a bigger size and dumping it into a bag without making a huge dust cloud is probably adequate.
- Keep in mind that if you are using a HEPA vacuum for other activities (lead paint, or asbestos) this will have other environmental impacts and cross-contamination (lead=TCLP, asbestos=haz waste disposal). I’d recommend having a silica-only vacuum.
- How do we make sure the dust is collected adequately?
- The short answer is, you should perform air sampling. I have performed a very limited amount of air sampling for tasks listed in Table 1, but they have all been below the detection limits. I have heard (not seen results) of some Table 1 tasks that were above recommended protection factors of Table 1.
- Another answer is that you should be following the manufactures’ instructions on the use of the tool and dust collection.
- How large should your silica “designated work areas” be when you set these up?
- I don’t have a straight forward answer to this, but I usually answer it by talking about those individuals who are “engaged” in the task, or not. I also mention there are many variables like; outdoor/indoor, task being performed, wind, etc.
- The bottom line is that if you are producing a lot of dust, you probably aren’t controlling the airborne silica, and you need to look at your controls, NOT how large or small your designated work area size.
- How do I know if my subcontractors are performing their silica tasks properly/adequately?
- This is a tough one because most General Contractor’s (GC) rely on their subs to do the work. However, all GCs must assure their subs are doing it correctly. The short answer is: do you see a dust cloud? If so, they’re doing it wrong.
- It would be best if all GCs review their subs silica exposure control plan and program prior to starting work. This should include the methods they will be using to control their silica tasks.
- It would also be beneficial to do job walks to verify subs are following their plan. AND, it would be awesome to catch them doing it right, and give THAT feedback.
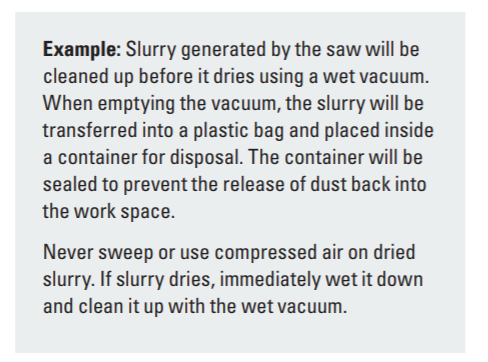